Lean Production: ottimizza l’efficienza del tuo Business
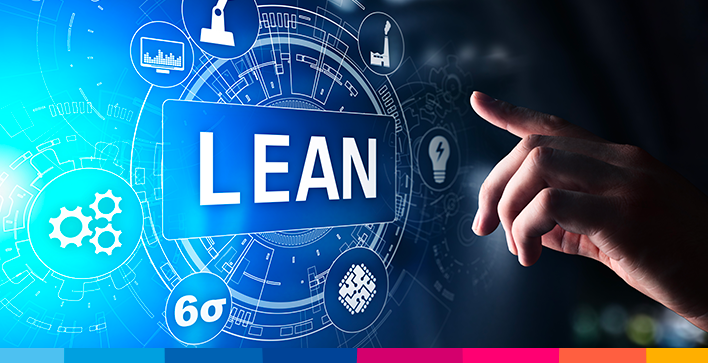
Non è facile chiedere a un esperto di parlare di lean production o lean manufacturing: su questo argomento ci si confronta infatti già da molti anni, ma la “produzione snella” è un concetto attualissimo e per nulla scontato in azienda.
Il Prof. Tommaso Rossi, docente presso LIUC – Università Cattaneo di Castellanza (VA) fornisce un punto di vista utile, originale e spassoso su questo tema, nel corso di un ciclo di incontri dal titolo “Impresa Possibile”.
Lean production: cos’è?
Non è semplice sintetizzare la Filosofia Lean: nel suo oltre mezzo secolo di storia, infatti, essa è sempre stata viva e si è via via arricchita arrivando a un mix di strumenti, di tecniche e di prassi piuttosto consistente. Ecco i due elementi fondamentali di tale filosofia produttiva per capire meglio cos’è la lean manufacturing.
1° elemento: la caccia agli sprechi
È piuttosto comune rappresentare il modello di riferimento della Filosofia Lean come un tempio greco più o meno ricco di colonne e di gradini che rappresentano tecniche e strumenti
Al centro del tempio, immancabile, c’è un cuore pulsante, un altare sul quale il Sacro Fuoco è sempre acceso: “la caccia agli sprechi”. Questo è il primo elemento fondamentale della Filosofia Lean: eliminare in azienda, e non solo in produzione, tutto ciò che è spreco, seguendo precisi modelli di analisi dei processi definiti di Business Process Improvement.
Cosa si intende per spreco nella filosofia lean?
Per Soichiro Toyoda, Chairman onorario di Toyota, è spreco ogni utilizzo di macchinari, materiali, manodopera e spazi che non aggiunge valore al prodotto, che non contribuisce a creare valore per il cliente.
È difficile dissentire dall’affermazione di Toyoda, ma alcune perplessità possono nascere su “come fare a individuare gli sprechi nel proprio sistema produttivo”.
Per il Prof. Rossi è molto calzante l’esempio di chi va a funghi per la prima volta.Iniziare da autodidatti ad andare a funghi è difficile: non si trova nulla, non si vede un porcino neanche a pagarlo! Ma se i primi tempi si va insieme a qualcuno che insegna a vedere i funghi tra le foglie secche, i ricci caduti e le felci, si imparerà a trovarli.
Ebbene il “fungiatt” al quale affidarsi per la caccia agli sprechi è Taiichi Ohno, l’iniziatore del “Toyota Production System”, che ha categorizzato gli sprechi e, così facendo, ci ha insegnato a vederli e, conseguentemente, a eliminarli.
Sette tipologie di spreco
In particolare, per Taiichi Ohno, le tipologie di spreco sono sette come i vizi capitali:
- spreco per sovrapproduzione, il cui sottostante è il concetto di lotto. Si produce più di quanto il cliente ha richiesto perché si è in qualche modo convinti che sia più conveniente produrre un multiplo di una certa quantità piuttosto che la quantità esatta ordinata dal cliente;
- spreco per movimenti risparmiabili: una non adeguata organizzazione dell’area di lavoro fa compiere passi inutili agli operatori e, come diceva sempre Taiichi Ohno, “un passo, un secondo, uno yen”;
- spreco per attese: il tempo che un prodotto attende a piè di macchina prima di essere lavorato in virtù del fatto che la macchina è al momento occupata è un tempo che non aggiunge alcun valore al prodotto in attesa ma che, in compenso, ne aumenta il lead time e, con esso, il work in process, lo spazio occupato in reparto e così via;
- spreco per scorte: produrre prodotti prima di quando lo richieda il cliente aumenta ovviamente il capitale immobilizzato;
- spreco per perdite di processo: sono uno spreco sia gli sfridi di materiale, sia gli sfridi di tempo;
- spreco per prodotti difettosi: sebbene in essi si sia immobilizzato un certo valore, non è possibile trarre alcun ricavo da tali prodotti perché invendibili presso i clienti. Conseguenza diretta di considerare i prodotti difettosi come uno spreco è quella di tendere ad avere zero difetti, di buttare a mare, insomma, il concetto di “percentuale accettabile di difettosità” e, ben consci della capacità del processo produttivo impiegato, introdurre gli aspetti di qualità in progettazione e di concurrent engineering;
- spreco per trasporto: è lo spreco noto anche con il termine di turismo aziendale; è esperienza comune che a volte i prodotti, per le ragioni più svariate, possano arrivare a compiere all’interno di uno stabilimento percorsi che superano di gran lunga l’estensione dello stabilimento stesso.
2°elemento: le persone
La caccia agli sprechi non potrebbe avvenire in modo efficace senza questo secondo elemento che è il coinvolgimento di tutte le persone all’interno dell’azienda.
Se fossero solo i manager (o, peggio ancora, solo i professori universitari o i consulenti) ad analizzare, per esempio, l’attività di cambio stampo su una pressa al fine di individuare gli sprechi annegati in tale attività ed eliminarli, ben pochi miglioramenti potrebbero essere attuati. È perciò necessario che le risorse intellettuali di tutto il personale dell’azienda siano mobilitate e poste al servizio dell’azienda stessa.
Le capacità degli uomini e donne d’azienda possono estendersi illimitatamente quando ogni persona comincia a pensare; è quindi evidente l’importanza del loro più totale coinvolgimento nella caccia agli sprechi seguendo i principi della lean organization. Una attività che, insieme a modifiche nel progetto del prodotto e/o a modifiche nelle macchine coinvolte nella produzione del prodotto stesso, è l’unica che consente di ottenere grandi e piccoli miglioramenti all’interno di un sistema produttivo
Production lean manufacturing: non sottovalutare i piccoli miglioramenti
Da non sottovalutare nella lean production manufacturing sono i piccoli miglioramenti perché, secondo Katsuaki Watanabe, uno dei past president di Toyota, “quando piccoli miglioramenti si accumulano per settanta anni, diventano una rivoluzione”. Nel pieno spirito del metodo Kaizen, che guarda ai processi di miglioramento continuo, infatti, anche i piccoli passi in avanti rappresentano un elemento positivo in grado di influenzare il futuro.
È dal coinvolgimento delle persone che passa il successo nel lungo periodo di una qualunque azienda. Ma come si fa? Le persone devono:
- essere trattate come esseri umani “intelligenti”;
- sentirsi parte essenziale nel raggiungimento degli obiettivi dell’azienda;
- essere ben addestrate e inserite in processi che permettano loro di lavorare bene e senza commettere errori;
- poter dare un contributo significativo al lavoro che svolgono (anche in termini di progettazione e riprogettazione delle procedure, degli spazi e delle attrezzature di lavoro);
- avere fiducia che il successo che hanno contribuito a ottenere si ripercuoterà positivamente su loro stesse.
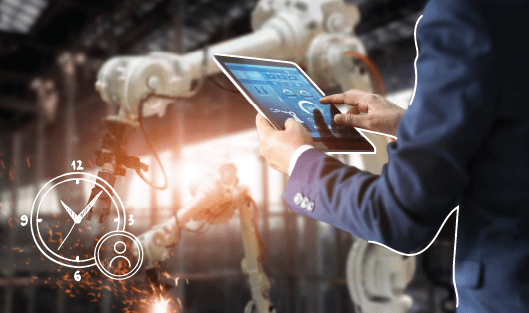