Cos’è un Gemello Digitale e a cosa serve
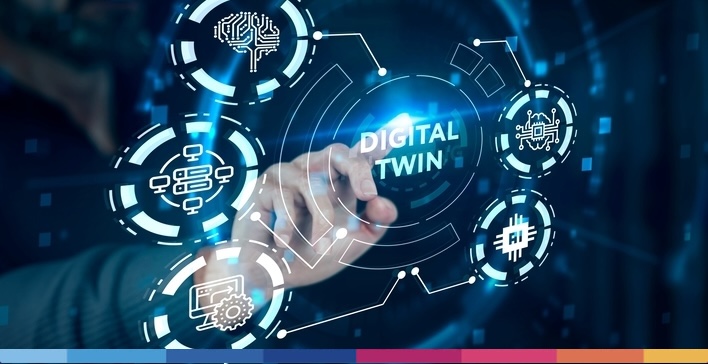
Rappresentano il futuro dell’Industria 4.0 e nei prossimi dieci anni guideranno l’innovazione tecnologica in vari settori: si tratta dei Gemelli Digitali (Digital Twin), ovvero riproduzioni virtuali di oggetti fisici (macchine, impianti, o addirittura un intero sistema industriale) che permettono di simulare e quindi ottimizzare i diversi processi produttivi, facendo previsioni sui cicli di vita dei macchinari e apportando miglioramenti costanti laddove necessario. Scopriamo cos’è un Gemello Digitale in ambito manifatturiero, come funziona e perché conviene.
Gemello Digitale – Digital Twin: cos’è
Un Gemello Digitale è la riproduzione virtuale di un oggetto fisico. A parlarne per la prima volta nel 2001 è Michael Grieves (Chief Scientist for Advanced Manufacturing al Florida Institute of Technology), che lo definiva come “l’equivalente virtuale di un prodotto fisico”. Si tratta di una rappresentazione dinamica e interattiva che si aggiorna in tempo reale grazie ai dati raccolti dai sensori installati sul dispositivo fisico ed elaborati da software di analisi avanzati e algoritmi di Intelligenza Artificiale. I Digital Twin consentono così di testare e prevedere con precisione il comportamento futuro dei prodotti che si intende realizzare, individuando eventuali anomalie e apportando i miglioramenti necessari. Tutto questo è possibile grazie all’integrazione di diverse tecnologie che fanno riferimento a un unico database dove vengono conservati tutti i dati di progettazione della macchina, le simulazioni e molto altro. Il Gemello Digitale contiene tutte le informazioni dell’oggetto fisico e può essere quindi utilizzato per:
- condurre attività sperimentali, come per esempio nel caso della creazione di un prodotto, che consente di risparmiare rispetto alla realizzazione di un prototipo fisico;
- fare delle simulazioni, analizzare le prestazioni di un prodotto e intervenire tempestivamente se si dovessero riscontrare comportamenti anomali.
Un Digital Twin integra quattro componenti fondamentali:
- il modello fisico dell’oggetto reale;
- i dati raccolti in tempo reale;
- gli algoritmi di simulazione e analisi predittiva, basati su Machine Learning e Intelligenza Artificiale;
- l’interfaccia di interazione, che consente agli operatori di visualizzare le performance e simulare scenari alternativi.
In questo modo i Gemelli Digitali permettono di replicare virtualmente l’intero ciclo di vita di un impianto o una macchina, dalla progettazione alla produzione, fino alla manutenzione predittiva e al fine vita.
Perché i Gemelli Digitali sono importanti
Il valore aggiunto dei Gemelli Digitali in ambito manifatturiero risiede nella loro capacità di anticipare i problemi prima che si verifichino, consentendo alle aziende di prendere decisioni più rapide e basate su dati concreti. Questo si traduce in una serie di benefici.
- Ottimizzazione dei processi produttivi. Il Digital Twin consente di monitorare in tempo reale le prestazioni delle apparecchiature e di identificare inefficienze o colli di bottiglia nella produzione. Le simulazioni permettono di testare modifiche ai processi senza interrompere la produzione reale e di risolvere i problemi via via che si verificano, riducendo i tempi di inattività e migliorando la produttività.
- Manutenzione predittiva. Grazie alla raccolta continua di dati e all’analisi predittiva, il Gemello Digitale può segnalare con largo anticipo guasti o anomalie di ogni componente o di un intero impianto. Un approccio “predictive maintenance” riduce i tempi di fermo macchina e allunga la vita degli impianti.
- Riduzione dei costi operativi. Attraverso la simulazione di vari scenari, le aziende possono individuare le soluzioni più efficienti in termini di risorse e consumo energetico, abbattendo così parte dei costi.
- Migliore efficienza. I Gemelli Digitali aiutano le aziende a monitorare i sistemi produttivi, anche dopo che un prodotto è entrato in produzione; in questo modo sarà possibile garantire la massima efficienza durante tutto l’arco del processo produttivo.
- Sviluppo di nuovi prodotti e personalizzazione. Un Gemello Digitale consente di testare nuovi prodotti prima ancora della loro realizzazione fisica, riducendo il time-to-market, ovvero il tempo che passa tra l’ideazione e la commercializzazione. Simulando configurazioni specifiche basate sulle esigenze individuali, consentirà inoltre di offrire ai clienti soluzioni personalizzate.
- Sostenibilità. Cosa fare dei prodotti che hanno raggiunto il loro fine vita? Anche in questo caso i Gemelli Digitali si rivelano alleati preziosi, indicando alle aziende quali materiali del prodotto possono essere raccolti e riciclati.
Digital Twin: esempi pratici
I campi di applicazione sono molteplici.
- Nel settore automobilistico, i Digital Twin vengono usati per progettare ed effettuare test virtuali sui veicoli per migliorarne design e prestazioni prima di finalizzarli e metterli in commercio. Questo consente di risparmiare sui costi altrimenti sostenuti per sviluppare dei prototipi fisici ed effettuare tutte le simulazioni necessarie. Ne sono un esempio Maserati e Ferrari.
- Alcuni brand di moda, come Gucci, hanno iniziato ad affidarsi ai Gemelli Digitali per la personalizzazione o la presentazione dei prodotti.
- Il Gruppo Cimbali usa i modelli digitali per migliorare le performance dei suoi prodotti, macchine per caffè.
- Biesse Group, produttore di macchine industriali, sfrutta i Gemelli Digitali per fornire ai propri clienti servizi di manutenzione predittiva.
I Gemelli Digitali rappresentano una straordinaria opportunità per il mondo dell’Industria 4.0, insieme a soluzioni sempre più all’avanguardia, come il software di ERP TeamSystem Enterprise per la gestione e semplificazione dei processi aziendali e la trasformazione dei dati in informazioni utili.
Grazie ad alcune specifiche funzionalità, permette alle aziende di ottimizzare l’intero ciclo produttivo, dall’approvvigionamento delle materie prime fino alla consegna del prodotto finito. Il modulo MES (Manufacturing Execution System) per esempio è in grado di migliorare la connettività tra le macchine, automatizzando i processi e riducendo gli sprechi. Raccoglie i dati di produzione passandoli direttamente dalla fabbrica all’ERP con strumenti dedicati agli addetti e alle macchine dei reparti produttivi.
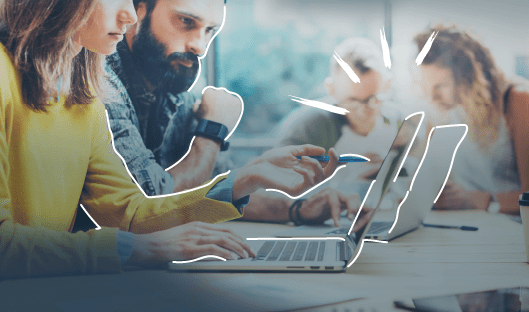